CASE STUDY
ROTOCON Ground Clamps Provide Quick ROI for Rotary Tank Welding Applications

Challenge
With over 100 years of experience in pioneering the compressor, air conditioning, refrigeration industry, Meridian Laboratory was approached by this manufacturer with challenges they faced in rotary tank welding applications. The company’s manufacturing process included using conventional brushed, rotary welding grounds.
Conventional brushed rotary grounds rely on metal on metal contacts to transfer current from the rotating to stationary portions of a machine. While simple in design and construction, there are numerous drawbacks associated with using conventional brushed rotary welding grounds. In fully and semi-automated rotational welding fixtures the machine relies on a fixed current setting to weld each seam. Over time, as a brushed rotary ground wears and changes in contact resistance, this increase in contact resistance leads to higher voltage drop and poor welding penetration. The end result is a greater amount of scrapped parts which did not meet the high-quality standards the manufacturer is known for.
Solution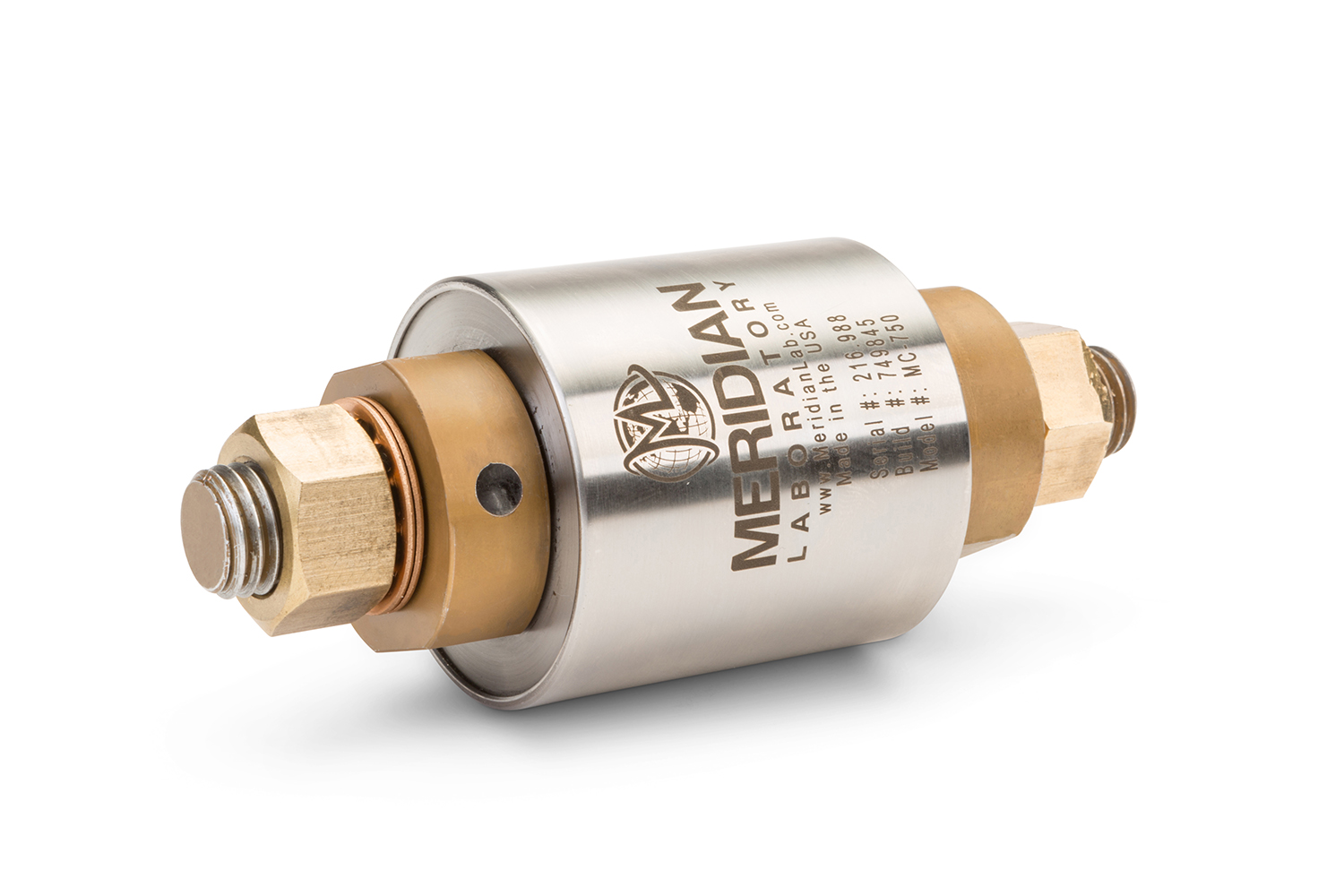
The company learned about Meridian Laboratory’s ROTOCON MC-Series rotary electrical grounds and the wide array of models, designs, and capabilities spanning from 250 to 10,000 amperes. They then retrofitted their existing equipment, replacing all brushed ground clamps with maintenance-free ROTOCON rotary grounds. After installation, the customer quickly realized the gains of consistent and level current flows while eliminating the greasing and maintenance.
Key Statistics
- Consistent and low contact resistance provided steady stable current flow
- 100% maintenance free and arc free design allows for uninterruptable machine output and usage
- Fewer defective end products provides quick return on investment