CASE STUDY
A Better Ground Clamp Solution: Switching to ROTOCON Rotary Ground Clamp Increases Productivity by 250%
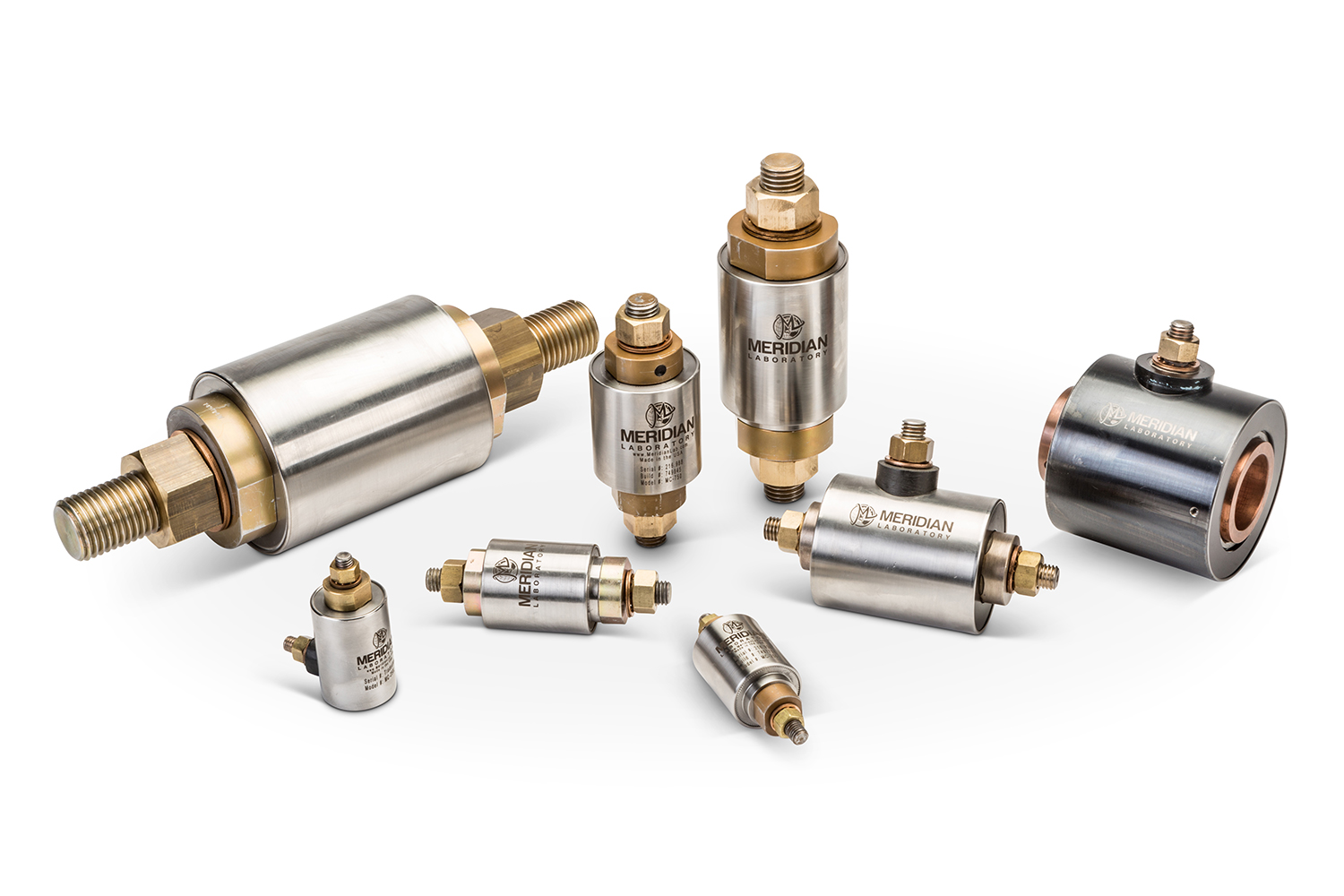
Challenge
A major manufacturer of outdoor power equipment, including garden tractors, lawn trimmers, and mowers approached Meridian Laboratory with challenges they faced using conventional brushed grounds for their automated rotary welding lines. Poor grounding caused inconsistent weld quality, pitting, and a lack of weld penetration of their end products. By converting their manufacturing lines to ROTOCON ERG Series rotary ground clamps they were able to alleviate all these issues and eliminate the downtime associated with greasing and maintenance required with brushed rotary grounds – ultimately increasing output productivity by 250%.
Historically, the manufacturer had relied on conventional, brushed rotary welding grounds for more than 20 years in their automated rotational welding equipment. While simplistic in design and operating principle, brushed rotary welding grounds have drawbacks associated to them including carbon build up, arc potential, duty cycle limitations, and periodic dielectric greasing is required to keep brushes maintained and functioning properly. These drawbacks ultimately lead to more downtime, poor weld quality, and overall decreased productivity.
Solution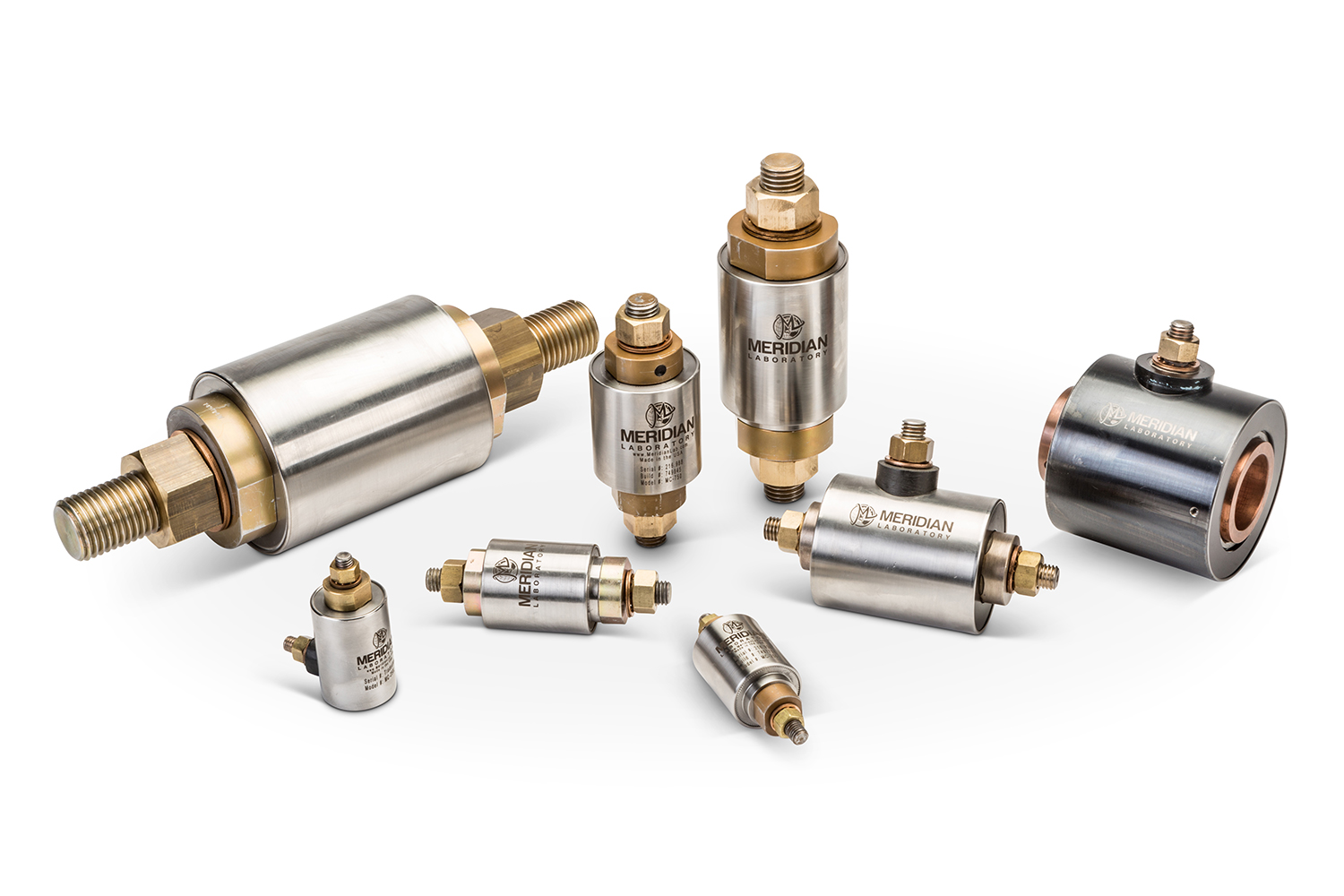
After learning about Meridian Laboratory’s ROTOCON high current, rotary ground clamp ERG Series, the customer was able to select from a variety of different models based on the current draw required in their rotary welding production lines. Utilizing standard, off-the-shelf, ROTOCON ERG models they were able to begin testing quickly and efficiently. The advantages were immediately noticeable in a more stable current flow, dramatically decreased pitting, and improved weld penetration and quality. They were able to decrease the amount of scrap products and increase output so quickly that the investment paid for itself within the first 30 days of usage. Long term, they were able to eliminate all previously routine scheduled maintenance breaks, which were associated with greasing and replacing conventional brushed rotary grounds. Since initial install and proof of concept, the manufacturer has now switched all of their rotary welding fixtures to ROTOCON ERG Series rotary ground clamps.
Key Statistics
- Eliminated inconsistent and poor weld penetration associated with conventional brushed rotary grounds
- Productivity increased by 250% by changing out brushed rotary grounds with ROTOCON, maintenance-free rotary grounds
- Drastically reduced scrap end products
About ROTOCON rotary ground clamps
Suitable for all environments and applications including welding, electro-plating, cutting, and other high current industrial applications, the ROTOCON ERG & ERGT Series is designed to withstand 100% duty cycles in continuous manufacturing and production processes. The ROTOCON’s brush-free design eliminates all issues such as maintaining brush contact, application of conductive greases, and the elevated contact resistance associated with conventional brushed rotary grounds. With the ERG Series, you will achieve a more consistent ground, with zero noise or elevated contact resistance over time and revolutions.
Unlike conventional brushed slip rings which rely on metal on metal contacts and are limited by RPM, electrically noisy, and require adjustment and maintenance for proper operation, all ROTOCONs are brushless, functioning through a molecularly bonded viscous metal film which remains unaffected by speed, provides clean and noise-free electrical signals, and requires zero maintenance.
The ERG Series is available both in end of shaft and through-bore configurations in a range of amperage levels, dependent on your needs. For applications requiring high frequency and high current, Meridian Laboratory offers specialized versions to accommodate for temperature rise due to eddy currents.
Watch the video below to see first hand the benefits which ROTOCON rotary grounds can provide.